Which is Better: Woven Interlining or Non-Woven Interlining
When it comes to enhancing the structure and durability of garments, choosing the right interlining can make a significant difference. Two popular options are woven interlining and non-woven interlining. Both have their own set of benefits and ideal applications. In this article, you will understand the differences between woven and non-woven interlining, so you can decide which is better suited for your projects. Let’s dive in and explore which type of interlining might be the best fit for your needs.
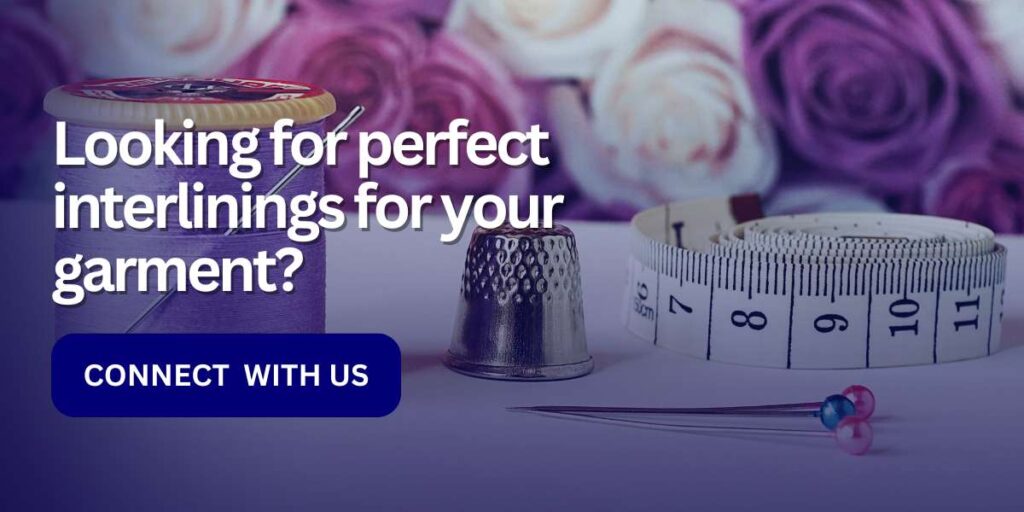
Table of Content
- What is Woven Interlining?
- What is Non-Woven Interlining?
- Comparing Woven and Nonwoven Interlining
- Key Differences Between Woven Interlining and Non-Woven Interlining
- How to Choose the Right Interlining for Your Needs
- Conclusion
What is Woven Interlining?
Woven interlining is created by weaving threads together in a crisscross pattern. This method results in a fabric that is structured and has a consistent pattern. Here’s what you need to know about woven interlining:
- Structure: Made by interlacing threads on a loom.
- Durability: Known for its strength and longevity.
- Texture: Typically has a grid-like pattern due to the weaving process.
Woven interlining is commonly used in garments where a firm structure and durability are required, such as in suits, jackets, and coats.
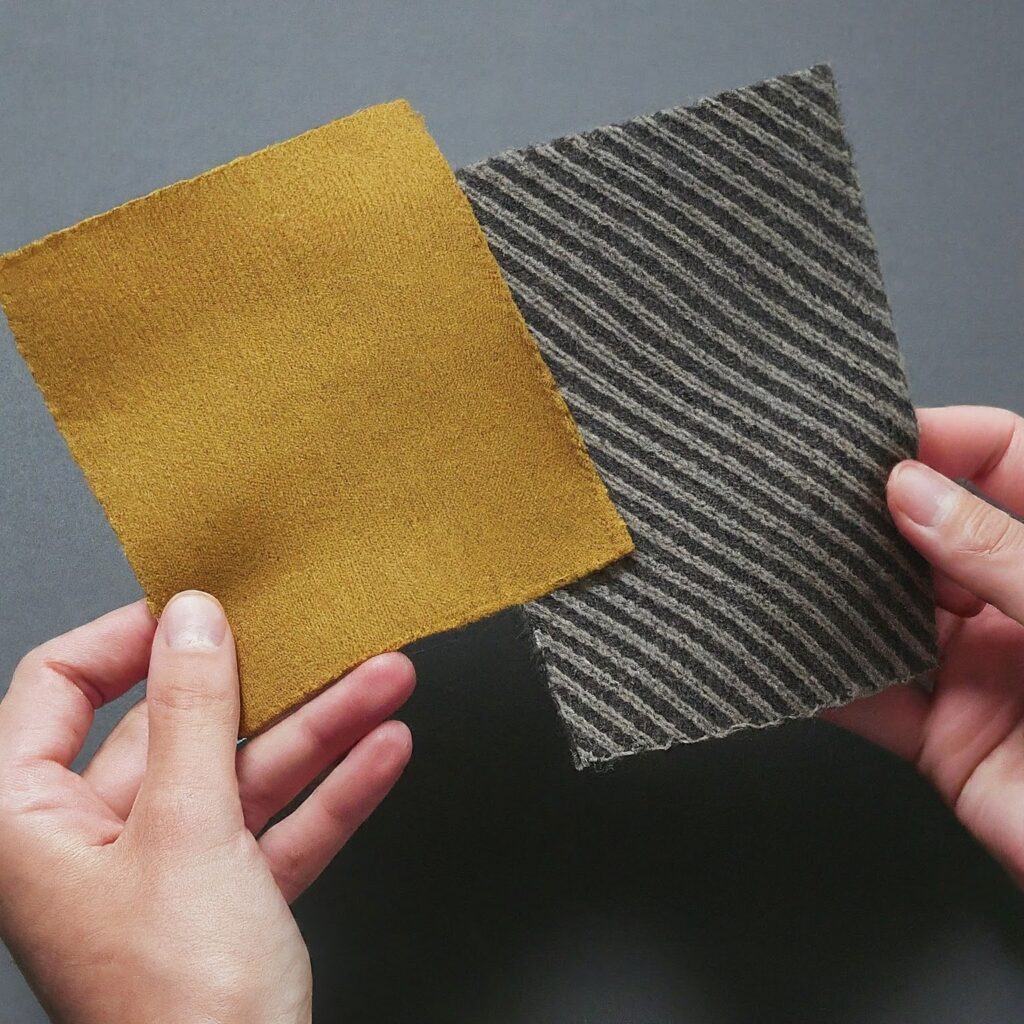
What is Non-Woven Interlining?
Non-woven interlining is produced by bonding fibers together using methods like heat, pressure, or adhesives, rather than weaving them. This results in a fabric that is usually softer and more flexible. Here’s what you need to know about non-woven interlining:
- Structure: Made by bonding fibers together.
- Versatility: Available in various weights and compositions.
- Applications: Often used in products like interfacing, filters, and disposable items.
Non-woven interlining is popular for its versatility and ease of use in various applications, including garments, home textiles, and crafts.
Features of Lightweight Interlining
- Thin and flexible: Perfect for maintaining the softness and drape of lightweight fabrics.
- Breathable: Does not add bulk or stiffness.
- Easy to work with: Ideal for projects where you need a light touch.
Comparing Woven and Nonwoven Interlining
Feature | Woven Interlining | Nonwoven Interlining |
Structure | Strong and rigid | Softer and more flexible |
Weight | Heavier | Lighter |
Cost | Generally higher | Generally lower |
Best for | Structured garments | Lighter garments |
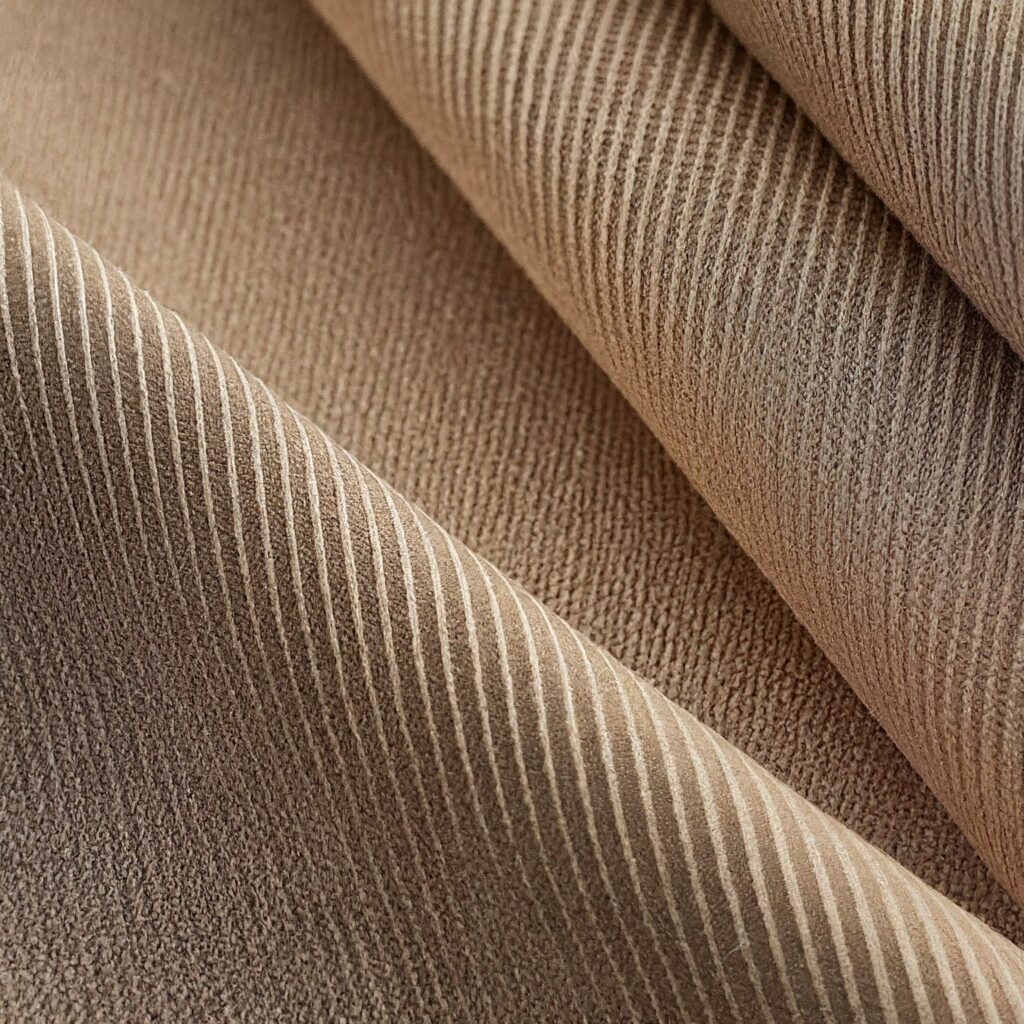
Key Differences Between Woven Interlining and Non-Woven Interlining
1. Structure and Durability
- Woven Interlining:
- Structure: Features a tight weave that provides strong support.
- Durability: Typically more durable and resistant to wear and tear.
- Maintenance: Can be prone to fraying and may require more care.
- Non-Woven Interlining:
- Structure: Fibers are bonded together, offering flexibility.
- Durability: Generally less durable but sufficient for short-term or disposable applications.
- Maintenance: More resistant to fraying and easier to clean.
2. Application and Versatility
- Woven Interlining:
- Applications: Ideal for applications requiring high durability and support, such as in jackets, suits, and formal wear.
- Versatility: Provides a structured finish, making it suitable for tailored garments.
- Non-Woven Interlining:
- Applications: Used in a wide range of applications, including interfacing, home textiles, and disposable products.
- Versatility: Works well in applications where flexibility and ease of use are important.
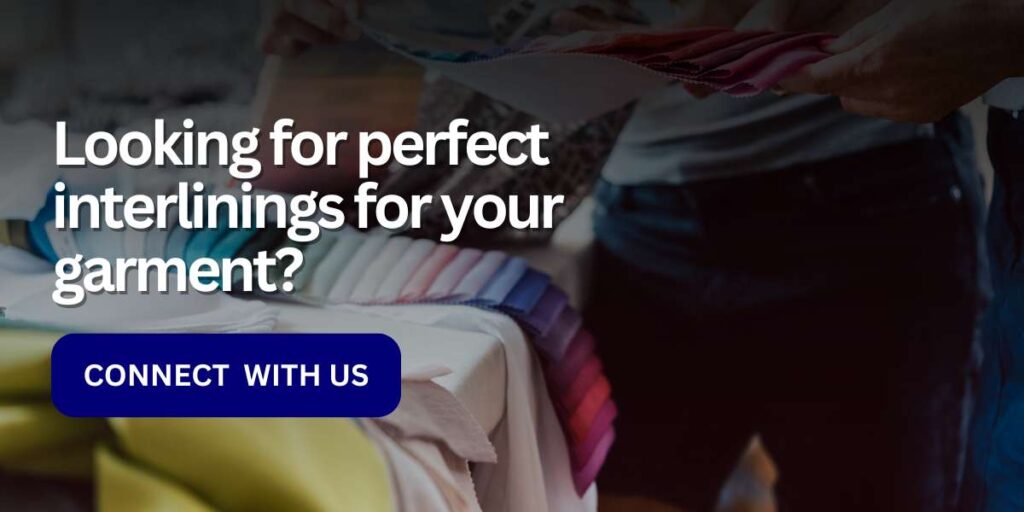
3. Comfort and Fit
- Woven Interlining:
- Comfort: Offers a more rigid structure, which might be less comfortable but provides a crisp and professional look.
- Fit: Helps garments maintain their shape and fit over time.
- Non-Woven Interlining:
- Comfort: Generally softer and more flexible, which can enhance comfort in certain garments.
- Fit: May not offer the same level of structure as woven interlining, but it provides a good fit for a range of applications.
4. Cost and Production
- Woven Interlining:
- Cost: Usually more expensive due to the complexity of the weaving process.
- Production Time: Takes longer to produce, which can affect turnaround times.
- Non-Woven Interlining:
- Cost: Typically more cost-effective due to simpler manufacturing processes.
- Production Time: Faster to produce, making it suitable for large-scale and quick production runs.
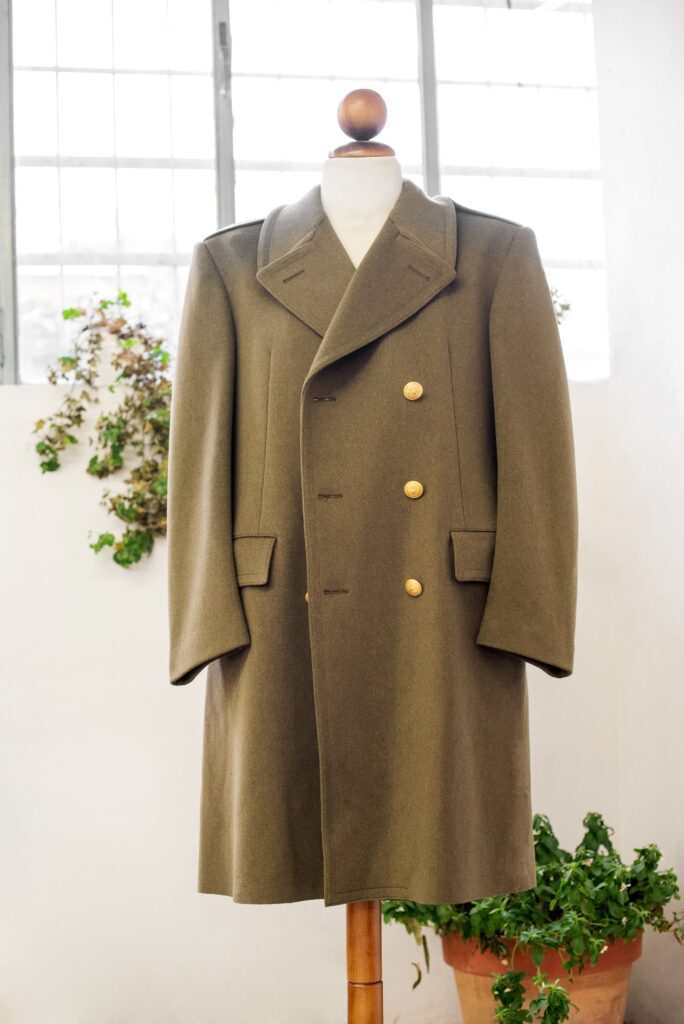
How to Choose the Right Interlining for Your Needs
When deciding between woven interlining and non-woven interlining, consider the following:
- Purpose: Determine if you need a rigid, durable structure (woven) or flexibility and cost-effectiveness (non-woven).
- Application: Choose based on the specific needs of your garment or project.
- Budget: Factor in the cost of materials and production, and choose accordingly.
Conclusion
Choosing between woven interlining and non-woven interlining depends on your specific needs and the type of project you’re working on. Woven interlining is great for high-durability applications where a structured finish is required, while non-woven interlining is ideal for more flexible, cost-effective solutions. By understanding the key differences and benefits of each, you can make the best choice for your project and ensure the best results.
Link of related Articles
- How to sew with non-woven interlining
- Techniques for using woven interlining for crisp edges
- Woven Interlining: The Classic Choice for Structured Garments
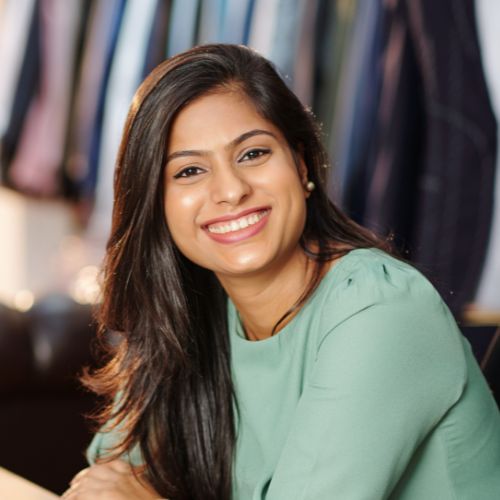