Which Button to Use on a Suit? | Essential Suit Buttoning Guide
When it comes to choosing the right button for your coat, the details matter. From style to function, the button coat you select can make or break your outfit. Whether you’re looking to update an old coat or design a new one, understanding the different types of coat buttons and their uses can enhance your wardrobe significantly. Let’s dive into the essentials of coat buttoning, so you can make informed choices that elevate your style.
Table of Contents
- Why Coat Buttons Matter
- Types of Coat Buttons
- Choosing the Right Button for Your Coat
- Maintaining Your Coat Buttons
- Conclusion
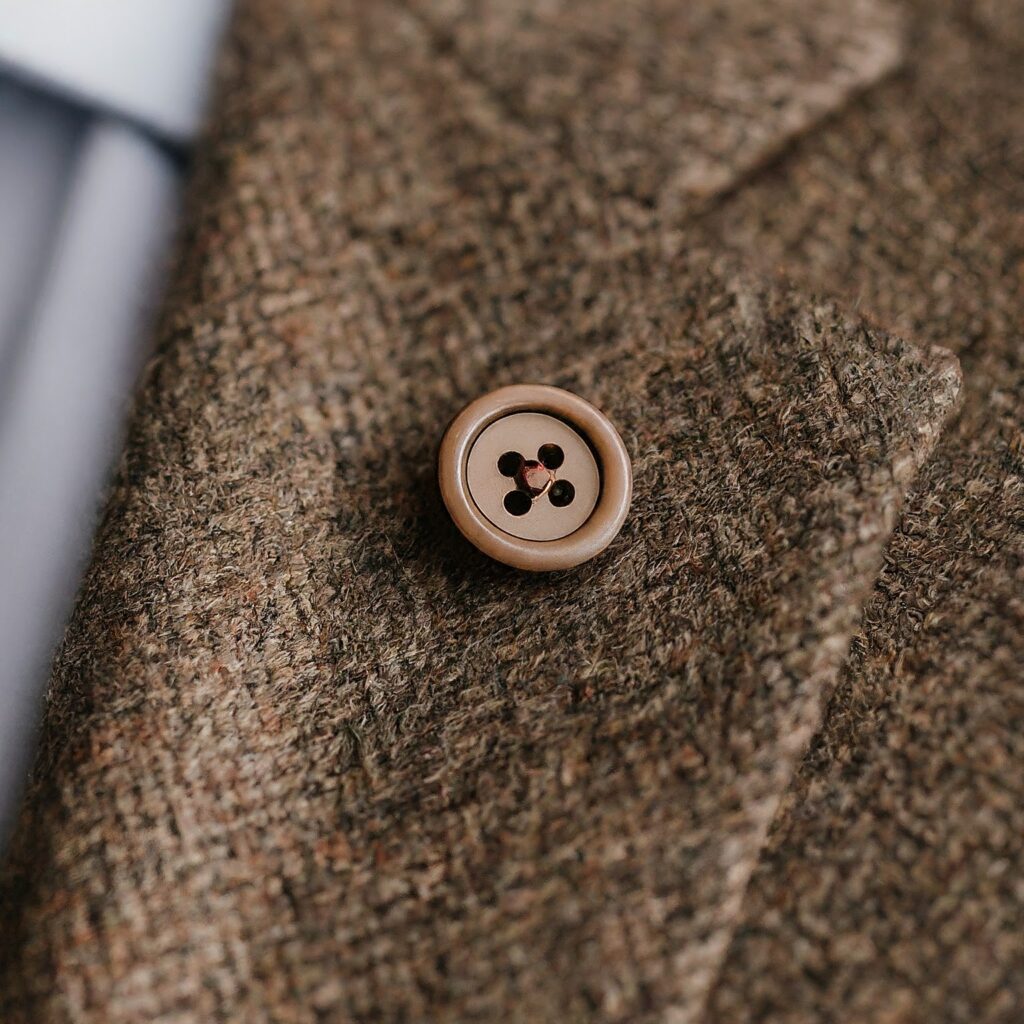
Why Coat Buttons Matter
Have you ever noticed how the right button coat can transform an ordinary coat into a fashion statement? It’s not just about aesthetics; coat buttons play a crucial role in both style and function. We have found the perfect button choice can enhance the overall look and feel of your coat, making it more versatile and stylish.
Here’s why buttons coat matter:
- Style Impact: Buttons are a focal point on any coat. They can either blend in or stand out, depending on your preference.
- Functionality: The right button coat ensures your coat stays securely fastened, providing warmth and protection against the elements.
- Personal Touch: Buttons offer a chance to showcase your personality and fashion sense.
Types of Coat Buttons
Understanding the different types of coat buttons is key to making the best choice for your coat. Let’s break down the most common types and their uses.
Functional Buttons
Functional buttons are more than just decorative; they serve a practical purpose. Here’s a closer look at these essential buttons:
- Dress Buttons: Often used on formal coats and jackets, these button coats are designed to complement the elegance of the garment.
- Military Buttons: Featuring detailed designs, military buttons are perfect for coats with a classic or historical style.
- Shank Buttons: These button coats are attached with a small stem, allowing them to be used on thicker fabrics or where extra space is needed.
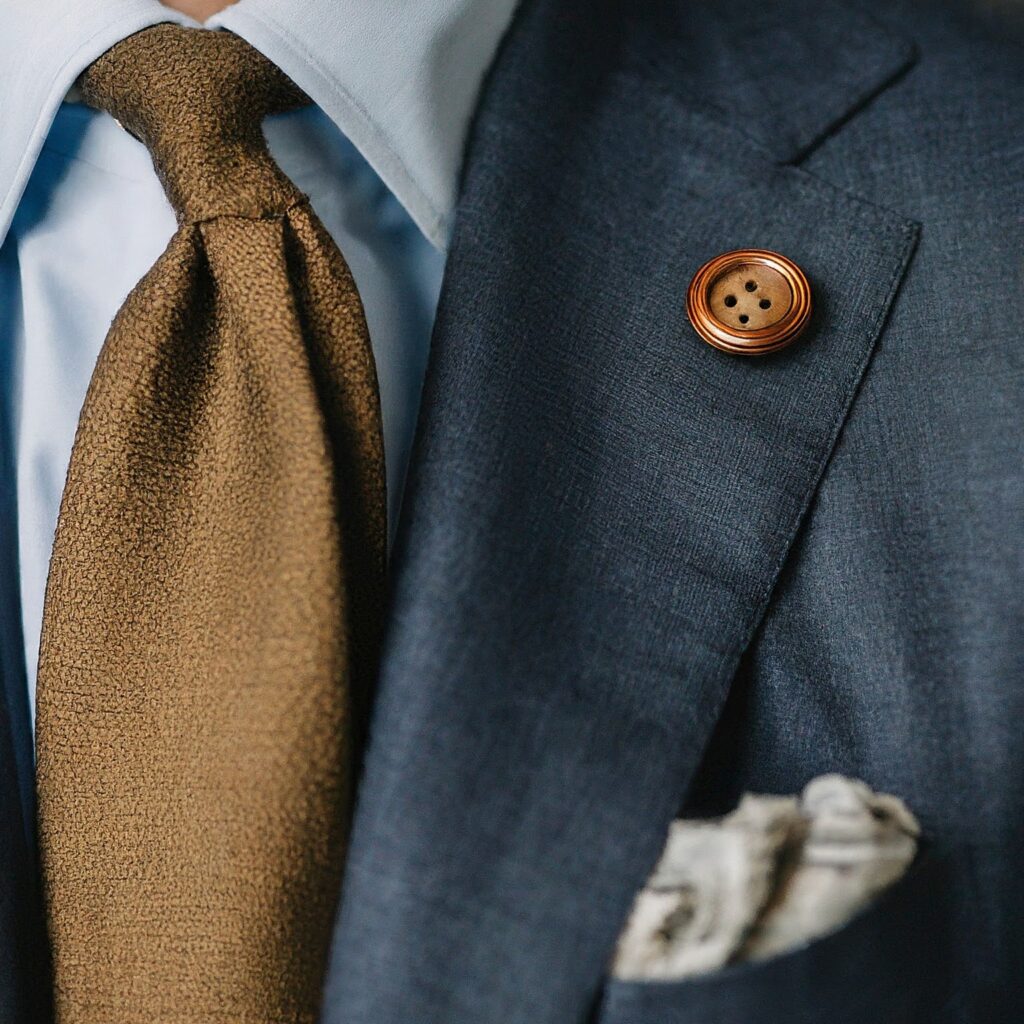
Decorative Buttons
Decorative button coats add flair and personality to your coat. They might not always serve a functional purpose but are great for enhancing your coat’s appearance:
- Novelty Buttons: These come in various shapes and designs, from quirky to elegant, and can be used to make a fashion statement.
- Covered Buttons: Made from the same fabric as the coat, covered buttons offer a seamless, sophisticated look.
- Gemstone Buttons: Embellished with gemstones or crystals, these button coats add a touch of luxury and sparkle.
Choosing the Right Button for Your Coat
Selecting the right button coats involves considering various factors, including material, size, shape, and placement. Here’s a guide to help you make the best decision.
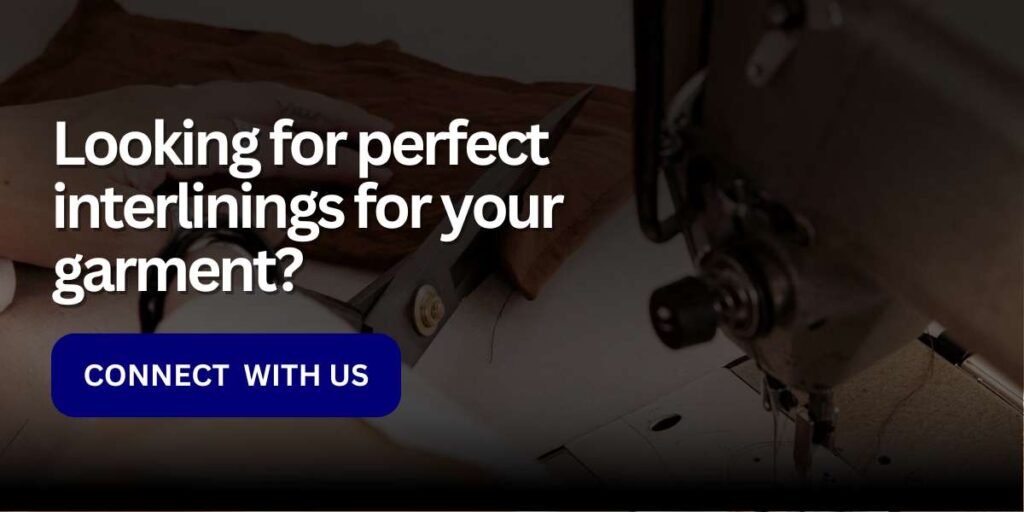
Material Matters
The material of your button affects both its appearance and durability. Here’s what you should know:
- Metal Buttons: Ideal for adding a touch of sophistication, metal buttons are durable and perfect for both casual and formal coats.
- Plastic Buttons: Affordable and versatile, plastic buttons can mimic other materials and come in many styles and colors.
- Wooden Buttons: Offering a natural and rustic feel, wooden buttons are great for casual or outdoor coats.
Size and Shape
The size and shape of your button should complement your coat’s design:
- Large Buttons: Best suited for overcoats and trench coats, large button coats make a bold statement.
- Small Buttons: Ideal for lighter fabrics or fitted coats, small button coats offer a subtle and refined look.
- Round Buttons: The most common shape, round buttons, work well for a variety of coat styles.
- Square and Oval Buttons: These shapes can add a unique touch to your coat, making it stand out from the crowd.
Button Placement
The placement of your buttons affects the overall look and functionality of your coat:
- Single-Breasted Coats: Typically have one row of buttons, providing a sleek and streamlined appearance.
- Double-Breasted Coats: Feature two rows of buttons, adding a layer of sophistication and warmth.
- High Placement: Buttons placed higher on the coat can enhance the visual appeal and provide a more fitted look.
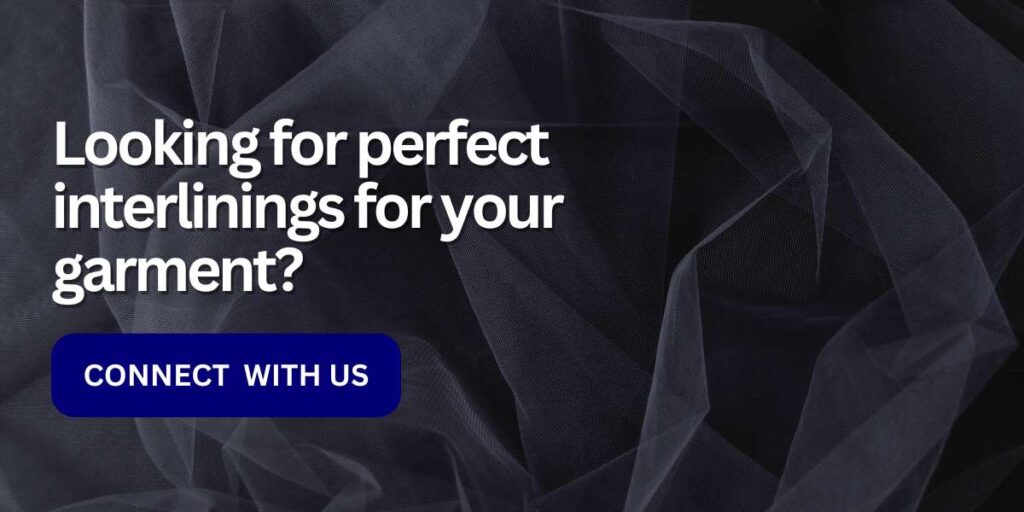
Maintaining Your Coat Buttons
To keep your coat looking its best, proper button maintenance is essential. Here’s how you can take care of your coat buttons:
- Regular Cleaning: Clean your buttons according to their material. Metal buttons may need polishing, while plastic ones can be wiped with a damp cloth.
- Repair Loose Buttons: If a button coat becomes loose, sew it back in place promptly to prevent losing it.
- Replace Damaged Buttons: If a button is cracked or broken, replace it with a similar one to maintain the coat’s appearance.
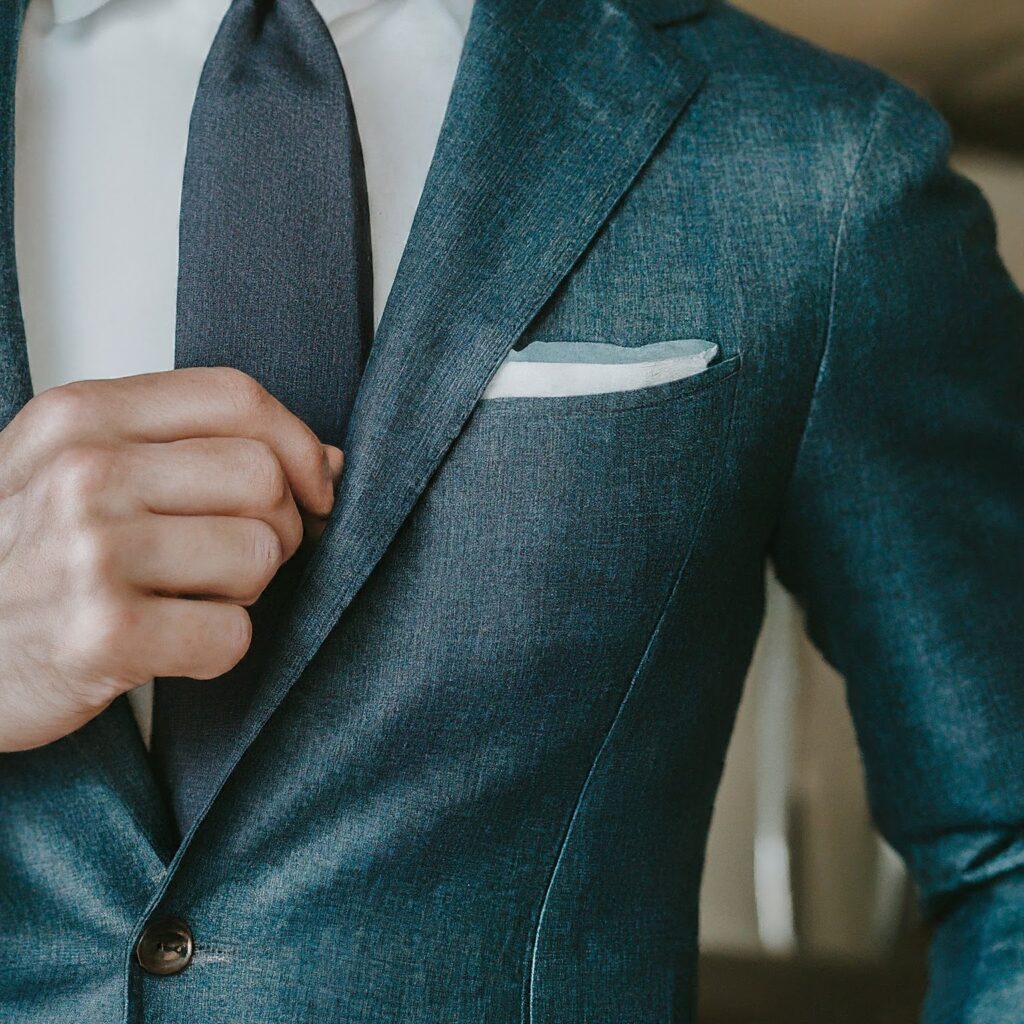
Conclusion
Choosing the right button for your coat can elevate your style and enhance the functionality of your garment. By understanding the different types of coat buttons, considering material, size, shape, and placement, and maintaining your buttons properly, you can ensure your coat remains both stylish and practical.
Remember, the details matter, and the right buttons for jackets or blazer buttons can make all the difference. I hope this guide helps you make informed choices and adds a touch of flair to your coat.
Happy buttoning!
Link of related Articles
- What Does the Name Buttons Mean? | Meaning & Origins Explained
- Blazer Buttons for a Special Occasion: Stylish Choices & Tips
- Peacoat vs Button Coat: Key Differences
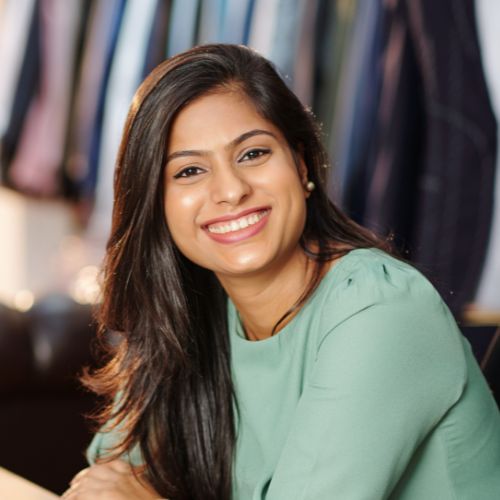